Critical decisions are made at the conceptual design stage in manufacturing. Several parameters determining product manufacturability are determined and locked in at this stage. The conceptual design stage incurs the least project cost relative to other downstream stages but helps to determine a significant percentage of the total production cost.
The early conceptual design phase in often focuses on functional requirements, with a limited consideration of the manufacturing processes that will be needed to turn design engineers’ conceptual models into physical products. In the past, design and manufacturing engineers often worked in close physical proximity. Today, the geographically distributed manufacturing paradigm has slowed the feedback cycle and increased product lead-time. Design for manufacturability (DFM) techniques have been adopted to overcome this problem. DFM feedback is critical for faster convergence to a manufacturable design.
The early conceptual design phase in often focuses on functional requirements, with a limited consideration of the manufacturing processes that will be needed to turn design engineers’ conceptual models into physical products. In the past, design and manufacturing engineers often worked in close physical proximity. Today, the geographically distributed manufacturing paradigm has slowed the feedback cycle and increased product lead-time. Design for manufacturability (DFM) techniques have been adopted to overcome this problem. DFM feedback is critical for faster convergence to a manufacturable design.
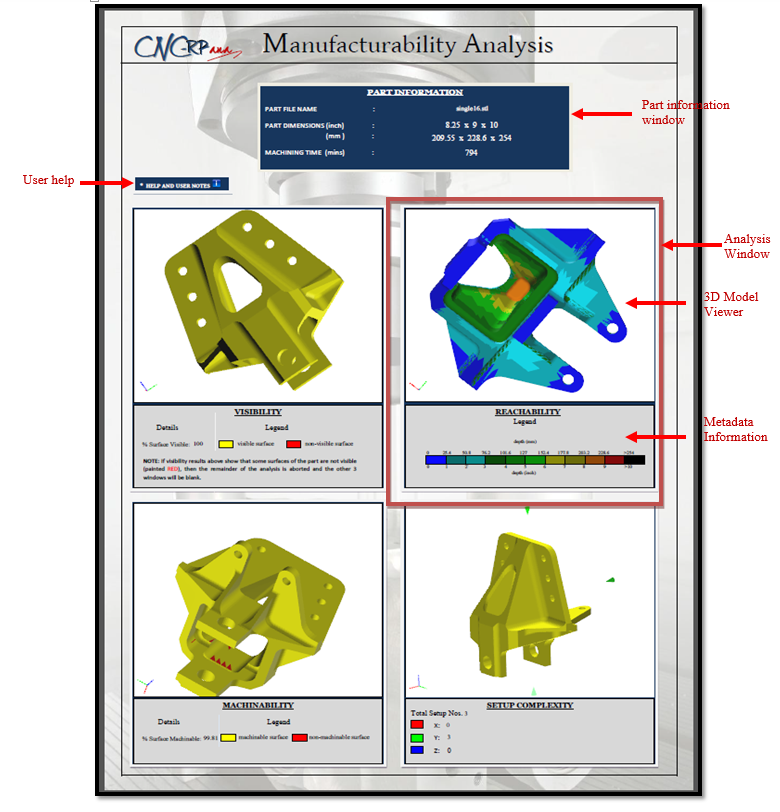
As part of a series of projects funded by DARPA and the Digital Manufacturing and Design Innovation Institute (DMDII), Iowa State and partners have developed a set of manufacturing process analysis tools for the early conceptual design phase, before tolerances and detailed dimensions have been fixed. The aim is to provide early manufacturing feedback for machining, casting, die-casting, and welding to novice design engineers.
As part of his MS thesis, Prashant Barnawal studied the most effective way to display and present this earl feedback to novice design engineers. DFM tools give feedback in several modalities, including textual and graphical. However, since information modality may affect interpretability, empirical evidence is needed to understand how manufacturability feedback modalities affect design engineers’ work. A user study was conducted with novice design engineers to evaluate how their design performance, workload, confidence, and feedback usability were affected by textual, two-dimensional (2D) and three-dimensional (3D) feedback modalities. Results showed that graphical feedback significantly improved performance and reduced mental workload compared to textual and no feedback. Differences between 3D and 2D feedback were mixed. 3D was generally better on average, but not significantly so. However, the usability of 3D was significantly higher than 2D. Conversely, providing feedback in textual modality was often no better than not providing any feedback. The study will benefit manufacturing industries by demonstrating that early 3D manufacturability feedback improves novice design engineers’ performance with less mental workload, and streamlines the design process resulting in cost-saving and reduction of product lead-time.
Under a DMDII project, the software package from the DARPA AVM tool suite will be matured to integrate manufacturability analysis elements created for the iFab Foundry and make them broadly available to design and manufacturing engineers. A dashboard has been developed to allow design engineers to compare and contrast earl design iterations across multiple manufacturing methods. PhD student Tor Finseth is leading the evaluation of the efficacy, validity, and adoptability of the software.
As part of his MS thesis, Prashant Barnawal studied the most effective way to display and present this earl feedback to novice design engineers. DFM tools give feedback in several modalities, including textual and graphical. However, since information modality may affect interpretability, empirical evidence is needed to understand how manufacturability feedback modalities affect design engineers’ work. A user study was conducted with novice design engineers to evaluate how their design performance, workload, confidence, and feedback usability were affected by textual, two-dimensional (2D) and three-dimensional (3D) feedback modalities. Results showed that graphical feedback significantly improved performance and reduced mental workload compared to textual and no feedback. Differences between 3D and 2D feedback were mixed. 3D was generally better on average, but not significantly so. However, the usability of 3D was significantly higher than 2D. Conversely, providing feedback in textual modality was often no better than not providing any feedback. The study will benefit manufacturing industries by demonstrating that early 3D manufacturability feedback improves novice design engineers’ performance with less mental workload, and streamlines the design process resulting in cost-saving and reduction of product lead-time.
Under a DMDII project, the software package from the DARPA AVM tool suite will be matured to integrate manufacturability analysis elements created for the iFab Foundry and make them broadly available to design and manufacturing engineers. A dashboard has been developed to allow design engineers to compare and contrast earl design iterations across multiple manufacturing methods. PhD student Tor Finseth is leading the evaluation of the efficacy, validity, and adoptability of the software.